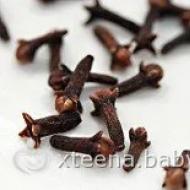
特別な濃縮方法。 濃縮法を使用した寄生虫の便の分析。 濃縮の種類とスキーム、およびその応用
機械式
主な鉱石選鉱プロセスには、鉱石の粉砕と精鉱の分離が含まれます。 粉砕では、通常は機械的方法によって天然素材を粉砕し、貴重な成分と不要な成分の粒子の混合物を生成します。 粉砕は、有用な原子を放出するために成分分子の化学分解によって補われることもあります。 分離または濃縮は、濃縮物と呼ばれる 1 つまたは複数の製品の有用な粒子を分離し、脈石の不要な粒子 (尾滓または廃棄物) を除去することで構成されます。 最終的に濃縮物にも廃棄物にもならない粒子は中間生成物と呼ばれ、通常はさらなる処理が必要です。
粉砕する鉱山から採取された岩石を、粉砕によるさらなる縮小に適したサイズに分解する機械的プロセスを指します。 鉱山から採掘された原材料を分解する装置は一次破砕機に分類されます。 その中で主なものはジョークラッシャーとコーンクラッシャーです。 二次粉砕は 1 段階、2 段階、またはそれより少ない頻度で 3 段階で行われます。
研削廃岩から有用な鉱物を機械的に分離する最終段階を表します。 通常、水生環境で、鋳鉄や鋼の球、フリント小石、鉱石や鉱石の硬い部分から形成された小石を使用して岩石を粉砕する機械によって製造されます。
ふるい分け濃縮のために供給される特定のサイズの材料を準備するために使用されます。 通常、スクリーンはサイズが 3 ~ 5 mm を超える粒子を分離します。 機械的分級機は、湿った材料と母岩をより細かく分離するために使用されます。
機械的分級機底が傾斜した長方形のトレイで、振動と往復運動をします。 粒子サイズによって分離される材料は水と混合され、分級機の上端に供給され、重力によってトレイの下端の凹部に移動されます。 そこでは、より重くて大きな粒子が底に沈み、コンベヤーによって取り上げられます。 軽くて小さい粒子は水の流れによって運び去られます。
遠心コーン分級機内水環境における遠心力は、鉱石粒子を分離するために使用されます。 このような分級機での分離プロセスにより、浮選によるさらなる濃縮に適した細粒の砂スラッジ画分を得ることが可能になります。
物理的な
機械的および物理的選鉱方法により、化学変換を行わずに純粋に物理的プロセスを使用して廃岩粒子から貴重な鉱石粒子を分離することが可能になります。
重力集中異なる密度の異なる鉱物の使用に基づいています。 異なる密度の粒子が、分離される鉱物の密度の中間の密度である液体媒体に導入されます。 この原理はおがくずを水に投入したときに砂が分離することで説明できます。 おがくずは水に浮き、砂は水に沈みます。
重環境下での濃縮方法これは、鉱石粒子に加えて、水と固体成分からなる懸濁液の使用に基づいています。 懸濁液の密度は、分離された鉱物の性質に応じて 2.5 から 3.5 まで変化します。 この場合、円錐形または角錐形の容器が使用されます。
治具- これは重力濃縮装置の一種で、懸濁液は水と鉱石粒子で構成されており、連続ジギングマシンには少なくとも 2 つの区画があります。 受入コンパートメントに入った重い粒子は底部に蓄積します。 軽い粒子が浮遊します。 供給された原料は流水に取り込まれ、斜面下部の表層に入り込み、エッジから飛び散りやすくなります。 しかし、重い物質は軽い物質を通って沈み、最下層にたどり着きます。 軽い素材が最上層と混合され、水の横方向の流れがそれを仕切りを通って隣接するコンパートメントに運びます。
分離。 自動アンロード装置は、必要な厚さを維持できる速度で最下層を除去します。
濃度表粒径 2.5 mm 未満の砂分画材料の処理に適した重力濃縮装置です。 その主要な要素は、リノリウムで覆われた幅 1.2 ~ 1.5 メートル、長さ約 4.8 メートルの長方形のデッキで、わずかに調整可能な横方向の傾斜を付けて設置され、毎分 175 ~ 300 サイクルの頻度で長辺に沿って往復運動します。振幅は 6 ~ 25 mm。
集中ゲート粗い底を持つ傾斜した溝で、それに沿って砂利(金を含むまたは錫を含む)が水の流れによって運ばれます。 この場合、重い鉱物はくぼみの底に沈んでそこに保持されますが、軽い鉱物は運び出されます。
浮選これは、鉱物の組成に応じた鉱物表面の物理化学的性質の違いに基づいており、これにより粒子が水中の気泡に選択的に付着します。 気泡と付着粒子からなる集合体は水面に浮き、気泡に付着していない粒子は沈降し、鉱物が分離されます。
磁気分離比較的高い磁化率を持つ鉱物を含む鉱石の選鉱に使用されます。 これらには、磁鉄鉱、フランクリン鉱、イルメナイト、磁硫鉄鉱、およびその他の鉄鉱物が含まれており、その表面には低温焼成によって望ましい特性を与えることができます。 分離は水性環境と乾燥環境の両方で実行されます。 乾式分離は大きな粒子に適しており、湿式分離は細粒の砂やスラッジに適しています。 従来の磁気選別機は、数粒子の厚さの鉱石の層を磁場中で連続的に移動させる装置です。 磁性粒子はベルトによって穀物の流れから引き出され、さらなる処理のために収集されます。 非磁性粒子は流れの中に残ります。
静電分離これは、電場の分極影響下にあるときに鉱物の表面全体に電子を伝達する、鉱物の異なる能力に基づいています。 その結果、異なる組成の粒子は、この磁場の強度とその曝露時間の特定の値で異なる程度に帯電し、その結果、同時に作用する電気力や他の力、通常は重力に対して異なる反応を示します。彼ら。 このような荷電粒子が自由に移動する機会が与えられると、それらの移動方向が異なり、それが分離に使用されます。
化学薬品
化学選鉱方法には、予備ステップとして鉱石の粉砕が含まれます。これにより、化学試薬が鉱石の貴重な成分にアクセスできるようになり、その後、これらの成分の抽出が促進されます。 化学的方法は、鉱石に直接適用することも、機械的方法による鉱石濃縮の結果として得られる精鉱の両方に適用することもできます。 化学濃縮法の用語はややわかりにくいです。 この記事の目的上、溶融分離は溶融プロセスを指し、選択的化学反応による分離は浸出プロセスを指します。
溶融高温で発生する化学プロセスであり、その間に貴重な金属と廃岩が溶解します。
燃焼浸出の準備として、有用な成分の化学組成を変更して浸出に適したものにするため、または特定の不純物を除去するために使用されます。特定の不純物の存在により、貴重な成分の浸出プロセスが大幅に複雑になり、コストが増加します。 たとえば、ヒ素と硫黄を含む一部の金鉱石は、浸出前に焙煎してこれらの成分を除去します。
浸出時鉱石の貴重な成分は溶解され、適切な溶媒によって不溶性残留物から分離されます。 場合によっては、貴重な成分を可溶性の形態に変換するために試薬が追加されます。
生物学的
細菌の導入
2ふるい分け 目盛り付きの穴のあるふるい表面(グリッド、シート、ワイヤーふるい)を使用して、塊状および粒状の材料をクラスと呼ばれるさまざまなサイズの製品に分離するプロセスです。
原料は篩い分けの結果、ふるい面の穴より粒(片)が大きい篩上製品(上製品)と篩下製品(下製品)に分けられます。 、その粒子(断片)はふるい面の穴のサイズよりも小さい。
粉砕と粉砕 – 外力の影響下で鉱物が所定のサイズ、必要な粒度組成、または必要な材料の開示度まで破壊されるプロセス。 粉砕および粉砕する場合、ミネラル濃縮のプロセスを損なうため、材料を粉砕しすぎてはなりません。
分類 – 水環境または空気環境での堆積速度に応じて、鉱物粒子の混合物をさまざまなサイズのクラスに分離するプロセス。 分級は、分離が水中環境で行われる場合 (水力分級)、分級機と呼ばれる特別な装置で行われ、分離が空気環境で行われる場合は空気分離器で行われます。
重力過程 濃縮とは、密度、サイズ、または形状が異なる鉱物粒子が、重力と抵抗力の影響下での環境内での移動の性質と速度の違いによって分離される濃縮プロセスを指します。
重力プロセスには、ジギング、重媒体での濃縮、テーブルでの濃縮、水門、シュート、ジェット濃縮器、コーン、スクリュー、向流分離器での濃縮、空気圧濃縮が含まれます。
浮選濃縮方法 – 細かく粉砕された鉱物を分離するプロセス。水性環境で実行され、天然または人工的に生成された水で湿る能力の違いに基づいて行われます。これにより、2 相間の界面への鉱物粒子の選択的付着が決まります。 浮遊選鉱における主要な役割は浮遊選鉱試薬によって演じられます。浮遊選鉱試薬は、特別な複雑さを伴うことなくプロセスを進めることを可能にし、浮遊選鉱プロセス自体と精鉱の収量を加速する物質です。
磁気濃縮法 鉱物は、分離された鉱物の磁気特性の違いに基づいています。 磁気特性に基づく分離は磁場中で行われます。
磁気濃縮中には、不均一な磁場のみが使用されます。 このような場は、セパレータの磁気システムの極の適切な形状と配置によって生成されます。 したがって、磁気濃縮は特別な磁気分離器で実行されます。
電気濃縮 鉱物の電気的特性の違いに基づいて、電場で鉱物を分離するプロセスです。 これらの特性は、電気伝導率、誘電率、摩擦電気効果です。
3.手動採掘と岩石サンプリング 濃縮方法としては、分離された鉱物の外部特性(色、輝き、粒子の形状)の違いを利用することに基づいています。 通常、鉱物の総質量から、含まれる量が少ない物質が選択されます。 鉱物から価値のある成分を選び出すことを採掘といい、廃石を採石といいます。
降水 これは、加熱およびその後の急速冷却時に個々の鉱物が亀裂 (破壊) する能力に基づいています。
摩擦、形状、弾力性の強化 これは、重力の影響下で平面に沿って分離された粒子が移動する速度の違いを利用することに基づいています。 傾斜面に沿った粒子の動きの主なパラメータは摩擦係数であり、これは主に粒子自体の表面の性質とその形状に依存します。
照度選別 、鉱物の放射性特性またはその放射線の強さの違いに基づいています。
放射濃縮法 さまざまな種類の放射線を放出、反射、吸収する鉱物のさまざまな能力に基づいています。
化学的濃縮方法へ これには、鉱物(またはその表面のみ)が他の化合物に化学変化し、その結果として鉱物の特性が変化したり、鉱物がある状態から別の状態に移行したりするプロセスが含まれます。
硫化物などのミネラルが酸化して強酸性溶液に溶解する能力に基づいた化学的および細菌の濃縮。 この場合、金属は溶液に入り、そこからさまざまな化学的および冶金学的方法を使用して抽出されます。 溶液中にチオン性細菌などの特定の種類の細菌が存在すると、ミネラルの溶解プロセスが著しく促進されます。
複雑な複合鉱石の濃縮のための技術スキームでは、重力と浮遊選鉱、重力と磁気など、2 つまたは 3 つの異なる濃縮方法が同時に使用されることがよくあります。また、湿式冶金法と組み合わせた複合濃縮方法も使用されます。
1 つまたは別の濃縮方法をうまく適用するには、この方法で使用される鉱物の特性に十分な違いがなければなりません。
4. 選鉱プロセスは、次の技術指標によって特徴付けられます。鉱石または選鉱生成物中の金属含有量。 製品の収率。 還元と金属回収の程度。
鉱石または選鉱製品中の金属含有量 - これは、乾燥した鉱石または製品の質量に対する、鉱石または濃縮製品中のこの金属の質量の比率をパーセンテージで表したものです。 金属含有量は通常、ギリシャ文字のα(元の鉱石中)、β(精鉱中)およびθ(尾鉱中)で表されます。 貴金属含有量は通常、質量単位(g/t)で表されます。
製品収率 - 濃縮中に得られた生成物の質量と、処理された元の鉱石の質量との比。単位またはパーセンテージの分数で表されます。 精鉱収量(γ)は、鉱石全体のどのくらいの割合が濃縮されているかを示します。
低減度 - 得られる精鉱の収量が処理された鉱石の量の何倍であるかを示す値。 低減度 (に)トン数を表します。 1 トンの精鉱を得るために処理する必要がある鉱石。次の式で計算されます。
K= 100/γ
非鉄およびレアメタルの鉱石は、精鉱の収率が低く、その結果、高度に還元されるという特徴があります。 濃縮収量は、直接計量するか、次の式を使用した化学分析に従って決定されます。
γ =(α - θ/β - θ)100,%。
濃縮度または濃縮度は、精鉱中の金属含有量が鉱石中の金属含有量と比較して何倍増加したかを示します。 貧弱な鉱石を濃縮する場合、この数字は 1000...10000 になる可能性があります。
金属回収ε - 精鉱中の金属の質量と元の鉱石中の金属の質量の比率をパーセンテージで表したものです。
ε=γβ/α
メタルバランス式
εα=γβ
プロセスの主要な技術指標を接続し、精鉱への金属抽出の程度を計算できるようにします。これにより、鉱石から精鉱への金属の移行の完全性が示されます。
濃縮生成物の収率は、生成物の化学分析から決定できます。 指定すると、 - 濃縮収量。 - 鉱石中の金属含有量。 - 濃縮物中の金属含有量。 - 尾鉱中の金属含有量、および - 精鉱への金属の抽出により、鉱石と濃縮製品の金属のバランスを計算することができます。つまり、鉱石中の金属の量は、精鉱と尾鉱中の金属の量の合計に等しくなります。
ここでは、元の鉱石の収率(パーセント)を 100 とします。 したがって、濃縮物の出力は
精鉱への金属回収率は、次の式を使用して計算できます。
濃縮収量が不明な場合は、
例えば、2.5%の鉛を含む鉛鉱石を選鉱すると、55%の鉛を含む精鉱と0.25%の鉛を含む尾鉱が得られます。 化学分析の結果を上記の式に代入すると、次のようになります。
濃縮収量
濃縮物への抽出
尾鉱出口
濃縮度:
定性的および定量的な濃縮指標は、工場における技術プロセスの技術的な完成度を特徴づけます。
最終濃縮製品の品質は、化学組成に関して消費者が設定した要件を満たさなければなりません。 濃縮物の品質に関する要件は規格と呼ばれ、GOST、技術条件(TU)、または暫定規格によって規制されており、この原料とその特性の処理技術と経済性を考慮して開発されます。 この規格は、最終濃縮製品中のさまざまな鉱物成分の最小または最大許容含有量を定めています。 製品の品質が規格を満たしている場合、その製品を規格と呼びます。
結論:
処理プラントは、鉱山(鉱山)と冶金プラントの間の中間リンクです。 鉱山から出てきた大小さまざまな鉱石は、処理工場で処理される際、目的に応じて準備、加工、補助に分けてさまざまな工程を経ます。
準備プロセスは、選鉱のために鉱石を準備することを目的としています。 準備には、まず第一に、鉱石片のサイズを小さくする操作、つまり破砕と粉砕、およびそれに関連するスクリーン、分級機、液体サイクロンでの鉱石の分級が含まれます。 粉砕中は貴重な鉱物の粒子をできるだけ開く必要があるため、最終的な粉砕サイズは鉱物の散在サイズによって決まります。
選鉱プロセス自体には、組成に含まれる鉱物の物理的および物理化学的特性に従って鉱石とその他の製品を分離するプロセスが含まれます。 これらのプロセスには、重力濃縮、浮選、磁気的および電気的分離などが含まれます。
ほとんどの濃縮プロセスは水中で行われ、得られる製品には大量の水が含まれます。 したがって、補助的なプロセスが必要になります。 これらには、濃縮、濾過、乾燥などの濃縮製品の脱水が含まれます。
さらに、次のようないわゆる特別なエンリッチメント方法もあります。
個々の鉱物の色や光沢、透明度や輝きの違いに基づいて採掘します。
鉱物の放射性特性や放射線の強さの違いに基づく、測度選別。
鉱物が平面に沿って移動するときの摩擦係数の違いに基づく摩擦濃縮。
硫化物などのミネラルが酸化して強酸性溶液に溶解する能力に基づいた化学的および細菌の濃縮。
選鉱プロセスは、鉱石または選鉱生成物中の金属含有量などの技術指標によって特徴付けられます。 製品の収率。 金属の還元と抽出の程度。これが濃縮プロセスの主な特性を決定します。
コントロールの質問:
1.
鉱物処理方法はどのセクションに分かれていますか?
2.
どの方法が濃縮の主要な方法とみなされ、どの方法が補助的な方法とみなされますか?
3.
どのような強化方法を知っていますか?
4.
ふるい分け、破砕、粉砕、分級のプロセスを説明します。
商業的に価値のある鉱物を見るとき、そのような魅力的なジュエリーを一次鉱石や化石からどのようにして作ることができるのかという疑問が当然生じます。 特に、岩石の加工自体が最終段階ではないにしても、少なくとも最終段階に先立つ精製プロセスであるという事実を考慮すると、 質問に対する答えは濃縮です。この濃縮では、空の媒体から貴重な鉱物を分離するなど、岩石の基本的な処理が行われます。
一般的な濃縮技術
貴重な鉱物の処理は特別な濃縮工場で行われます。 このプロセスには、準備、直接分割、不純物を含む岩石の分離など、いくつかの操作を実行することが含まれます。 濃縮中に、黒鉛、アスベスト、タングステン、鉱石材料などを含むさまざまな鉱物が得られます。これらは必ずしも貴重な岩石である必要はありません。原材料を処理し、後で建設に使用する工場がたくさんあります。 いずれにせよ、鉱物処理の基本は鉱物の特性の分析に基づいており、分離の原理も決定されます。 ところで、さまざまな構造を切断する必要性は、1つの純粋な鉱物を取得するためだけではありません。 複数の貴重な品種が 1 つの施設から飼育されるのが一般的です。
岩石破砕
この段階で、材料は個々の粒子に粉砕されます。 粉砕プロセス中に、内部の接着メカニズムを克服するために機械的な力が使用されます。
その結果、岩石は均質な構造を持つ小さな固体粒子に分割されます。 直接粉砕技術と粉砕技術を区別する価値があります。 最初のケースでは、鉱物原料はそれほど深くは構造の分離を受けず、その間に 5 mm を超える部分の粒子が形成されます。 次に、研削により直径 5 mm 未満の要素が確実に形成されますが、この指標は扱う岩石の種類によって異なります。 どちらの場合も、課題は、有用物質の粒子の分割を最大限に高め、純粋な成分、つまり廃岩や不純物などが混合せずに放出されるようにすることです。
審査の流れ
破砕プロセスの完了後、収穫された原材料は、ふるい分けや風化などの別の技術的影響を受けます。 スクリーニングは本質的に、得られた粒子をそのサイズ特性に従って分類する方法です。 この段階を実行する従来の方法では、セルを校正する機能を備えたふるいおよびふるいを使用します。 スクリーニングプロセス中に、オーバーグリッド粒子とアンダーグリッド粒子が分離されます。 不純物や混合物の一部が分離されるため、何らかの形でミネラルの濃縮がこの段階で始まります。 サイズが 1 mm 未満の小さな断片も、風化によって空気の助けを借りてふるい分けられます。 細かい砂を思わせる塊が人工気流によって持ち上げられ、沈降します。
その後、よりゆっくりと沈降する粒子が、空気中に残留する非常に小さな粉塵要素から分離されます。 このようなスクリーニングの誘導体をさらに収集するには、水を使用します。
強化プロセス
濃縮プロセスは、原料から鉱物粒子を分離することを目的としています。 このような手順では、有用な濃縮物、廃棄物尾鉱、その他の生成物など、いくつかのグループの要素が分離されます。 これらの粒子を分離する原理は、有用鉱物と廃岩の性質の違いに基づいています。 このような特性には、密度、濡れ性、磁化率、サイズ、導電率、形状などがあります。したがって、密度の違いを利用する濃縮プロセスでは、重力分離法が使用されます。 このアプローチは、鉱石および非金属原料に使用されます。 コンポーネントの湿潤特性に基づいて強化することも非常に一般的です。 この場合、微粒子を分離できるのが特徴の浮選法が用いられます。
鉱物の磁気濃縮も使用されており、タルクやグラファイト媒体から鉄不純物を分離したり、タングステン、チタン、鉄、その他の鉱石を精製したりすることが可能になります。 この技術は、化石粒子に対する磁場の影響の違いに基づいています。 使用される装置は、マグネタイト懸濁液の回収にも使用される特殊な分離装置です。
濃縮の最終段階
この段階の主なプロセスには、脱水、パルプの濃厚化、および得られた粒子の乾燥が含まれます。 脱水装置の選択は、鉱物の化学的および物理的特性に基づいて行われます。 原則として、この手順は複数のセッションで実行されます。 ただし、その実装の必要性が常に発生するとは限りません。 たとえば、濃縮プロセスで電気的分離が使用された場合、脱水は必要ありません。 さらなる処理プロセスのために濃縮製品を準備することに加えて、鉱物粒子を扱うための適切なインフラストラクチャを提供する必要があります。 特に、工場は適切な生産サービスを組織します。 店舗内車両を導入し、水・熱・電気の供給を整えています。
選鉱設備
粉砕および破砕段階では、特別な設備が使用されます。 これらは、さまざまな駆動力の助けを借りて、岩石に破壊的な影響を与える機械ユニットです。 次に、ふるい分けプロセスでは、ふるいとふるいが使用され、穴を校正する可能性が提供されます。 ふるい分けには、スクリーンと呼ばれるより複雑な機械も使用されます。 直接濃縮は、構造分離の特定の原理に従って使用される電気、重力、磁気分離器によって実行されます。 この後、排水技術が脱水に使用され、その実装では同じスクリーン、エレベーター、遠心分離機、濾過装置を使用できます。 最終段階では、原則として、熱処理と乾燥剤の使用が行われます。
濃縮プロセスからの廃棄物
濃縮プロセスの結果、いくつかのカテゴリーの製品が形成され、有用な濃縮物と廃棄物の 2 つのタイプに分類できます。 さらに、価値のある物質は必ずしも同じ岩石を表す必要はありません。 また、廃棄物は不要な物とは言えません。 このような製品には貴重な濃縮物が含まれている可能性がありますが、その量は最小限です。 同時に、廃棄物構造内にある鉱物をさらに濃縮することは技術的にも財政的にも正当化されないことが多く、そのような処理の二次プロセスはほとんど実行されません。
最適な濃縮
濃縮条件、出発物質の特性、および方法自体によって、最終製品の品質は異なる場合があります。 有価成分の含有量が多く、不純物が少ないほど良いとされます。 たとえば、理想的な鉱石選鉱には、製品中に廃棄物が完全に存在しないことが含まれます。 これは、破砕およびふるい分けによって得られた混合物を濃縮する過程で、廃岩からのデブリ粒子が全質量から完全に排除されたことを意味します。 ただし、そのような効果を常に達成できるとは限りません。
鉱物の部分選鉱
部分濃縮とは、化石のサイズクラスを分離すること、または生成物から不純物の容易に分離される部分を切り取ることを指します。 つまり、この手順は、製品から不純物や廃棄物を完全に取り除くことを目的としたものではなく、有用な粒子の濃度を高めることによって原料の価値を高めるだけです。 鉱物原料のこのような処理は、例えば石炭の灰分を減らすために使用できます。 濃縮プロセス中、濃縮されていないスクリーニングの濃縮物と微細画分をさらに混合すると、大規模な種類の元素が分離されます。
濃縮中の貴重な岩石の損失の問題
不要な不純物が有用な精鉱の塊の中に残るのと同じように、貴重な岩石も廃棄物と一緒に除去することができます。 このような損失を考慮するために、特別なツールを使用して、各技術プロセスの許容レベルを計算します。 つまり、許容損失に関する個別の基準がすべての分離方法に対して開発されています。 許容パーセンテージは、水分係数と機械的損失の計算における誤差をカバーするために、加工製品のバランスに考慮されます。 このような計算は、深度破砕が使用される鉱石の選鉱が計画されている場合に特に重要です。 したがって、貴重な濃縮物を失うリスクが増加します。 しかし、ほとんどの場合、有用な岩石の損失は技術プロセスの違反によって発生します。
結論
最近、貴重な岩石を濃縮する技術の発展は目覚ましいものがあります。 個々の処理プロセスと一般的な分離スキームの両方が改善されています。 さらなる進歩に向けた有望な方向性の 1 つは、濃縮物の品質特性を改善する複合処理スキームの使用です。 特に磁気分離器を組み合わせることで、最適化された濃縮プロセスが実現します。 このタイプの新しい技術には、磁気流体力学的分離と静磁気流体分離が含まれます。 同時に、鉱石が劣化する一般的な傾向もあり、得られる製品の品質に影響を与えざるを得ません。 不純物のレベルの増加は、部分濃縮を積極的に使用することで対処できますが、一般に、処理セッションが増加すると、この技術の効果はなくなります。
鉱物の破壊は抽出中に始まります。 鉱物は、形成条件とその後の変成現象に応じて、異なる性質を持ちます。 特定の抽出および輸送方法を使用すると、ミネラルは、サイズ、強度、硬度、弾性が異なる穀物の混合物の形で加工工場に届けられます。
多くの鉱物では、分離された鉱物の物理的および機械的特性 (ヤング率およびポアソン弾性率、強度) の違いにより、粉砕および粉砕のプロセス中に、さまざまな鉱物の粒子のサイズと形状が大きく異なるという事実が生じます。 一部の著者は、これをミネラル強度に基づく濃縮と呼んでいます。 採掘プロセスや鉱山内でのその他の作業中の鉱物と母岩の強度に応じて、出発原料はさまざまなサイズの粒子で構成され、クラスに分けられると、有用な成分と汚染物質の両方の含有量が異なる製品になります。入手できます。 たとえば、磁鉄鉱珪岩を粉砕する場合、粉砕された製品中のより強い石英はマグネタイトよりも大きなグレードになります(選択的な粉砕と粉砕)。
サイズ分離は、出発原料の個々のクラスの品質に違いがある場合に使用されます。 ここでは、乾式(塵除去用)と湿式(液体サイクロン、遠心分離機)の両方の遠心装置を使用する必要がある場合があります。 このプロセスは、独立(ディスク分離機上)または付随(たとえば、スクリーニング中、空気圧および湿式分級、ルーバー装置、遠心除塵機、液体サイクロンなど)のいずれかで行うことができます。
適切な準備をしたこの方法による濃縮は、貴石(ダイヤモンド)の濃縮など、抽出生成物を大きな形で取得する必要がある場合、または高度に分散した粘土の濃縮など、微細な物質の形で取得する必要がある場合に実行されます。 。
すでに示したように、一部の鉱物の強度または硬度の強化は、衝撃を使用した破砕、粉砕、または摩耗によって実行されます;鉱物を開くより選択的な方法については、以下の特別なセクションで説明します。
前述の種類の粉砕の結果、より硬い岩石を含む原石炭が濃縮されるだけでなく、同じ比重を持つこの砂利に含まれる砂利よりも摩耗しにくいブラック ダイヤモンドを含む砂利が濃縮されます。ダイヤモンドのように。
メートル、そして移動するとき - 重量 Q = mg。
一部の鉱物の抽出および加工中に、その成分の破片の形状の違いも観察されます(石炭、頁岩、雲母、およびアスベスト含有鉱石では、成分の破片の形状の違いは、それらの物理的影響の結果です)プロパティ)。 形状によって粒子を分離すると、分離生成物中の 1 つまたは別の成分が濃縮されます。 混合物に含まれる形状の異なる成分の分離(たとえば、無煙炭に伴う層状岩の分離、またはアスベスト鉱石中の針状アスベスト繊維の分離)は、他の操作(分級、脱水など)を実行する装置でも同時に発生する可能性があります。 。)。
これらの異なるプロセスを接続する共通のリンクは、分離器または分類器の作業面です。 最後は、異なるふるい面を備えたスクリーンです。サイズによる分離の場合は、所定のセル サイズが必要です。形状による分離の場合は、サイズだけでなく、ピースの特性に応じて穴の形状も重要です。分離されたミネラルのこと。
サイズごとに充実。このような濃縮の可能性は、分離された鉱物の物理的および機械的特性によるものです。 したがって、たとえば石炭採掘では、岩石が強ければ、より大きな種類の原料ほど灰分が多くなります (表 4)。
リン鉱石中の P 2 O 5 クラスの分布を表に示します。 8.5。
さまざまなサイズの初期製品のクラスの収量とその品質は、ふるい分析と技術分析を使用して決定されます。 濃縮能力および考えられる濃縮結果は通常の方法で決定できます。この目的のために、表が作成され、濃縮曲線がプロットされます。
洗浄性曲線を作成するには、灰分または P 2 O 5 含有量の増加順にクラスを表に記録する必要があります。
細かさの違いは、母材の選択的な風化に起因する可能性があります。
場合によっては、このプロセスは独立した重要性を持つことがあります。 たとえば、風化した後にダイヤモンド鉱石を選別すると、一次ダイヤモンド精鉱が生成されます。
このプロセスは、他の宝石の抽出にも使用できます。
原料物質の他の種類の前処理も、そのサイズに応じて、混合物の鉱物成分の品質に大きな違いをもたらす可能性があることに注意する必要があります。 これらには、加熱、冷却、弾性粉砕、鍛造などが含まれます。
サイズ別に選鉱する場合、そのプロセスは有用な鉱物の含有量が異なる異なるサイズの粒子の分離に関連するため、明らかに粒子の質量を考慮する必要があります。 メートル、そして移動するとき - 重量 Q = mg。
選択的スクリーニングを使用して粒度分離を行う場合、あるサイズの粒子の重量が増加することが好ましい要因となる。 この場合、粒子が篩の穴を通過する可能性は、粒子と穴の大きさの比によって決まります。
粒子サイズを濃縮するには、水平ディスク分離機を使用できます。その設計と操作を図に示します。 2.4.1.
分離プロセス中、より大きな粒子はより大きな遠心力を持ち、より遠くまで飛ばされ、同心円状の受け器に落ちます。 Ⅱ。 小さな粒子はディスク D からレシーバーに落下して収集されます。 私。 この装置は、主にディスクの回転数を変更することによって調整および制御されます。これにより、遠心力と粒子がディスクの表面から離れる速度が変化します。また、粒子源の運動量も変更されます。装置に供給される材料。
![]() |
場合によっては、粉砕機などの濃縮機械の操作の特殊性により、粒子の形状の違いが観察されることがあります。 そのため、建設用に岩石を砕いて砕石を作ると、砕石中に「フレーク」(板状)の粒子が発生し、砕石をコンクリートの充填材として使用した場合、強度が低下します。 最終製品中の「フレーク状」粒子の含有量を減らすことが考えられます。 米。 2.5.1 砕石の品質を向上させる。
さまざまな形状の粒子の線形サイズの比率 (単位の割合) (V. G. Derkach および P. A. Kopychev による) を以下に示します。
長さ 幅 厚さ
粒子形状:
ラメラ...1 1(0.75) 0.5
長方形…1 0.5 0.5
角度.... 1 1 0.5
丸い.... 1 1 1
コンポーネントの形状の違いを利用して粒子を分離するには、次の方法を使用できます。
特別に設計されたスクリーニング表面でスクリーニング。
異なる形状の粒子の摩擦係数の違いを利用した濃縮。
粒子の形状の違いによる媒体中の粒子の移動速度に応じた分離。
装置の作業面と粒子の接触面積に応じた分離;
組み合わせた分離方法。
円形から正方形へ、正方形から長方形へ、長方形からスロット状の穴に移行すると、スクリーニングによる板状または細長い粒子の分離が向上します。 分別された品質の向上
「フレーク状」形状の粒子が放出されるため、高品質の砕石は、ゴム紐のふるい分け表面を使用することによって、つまり、正方形の穴から長方形の穴への移行を使用することによって達成されます。 。
フォームを強化するためのセパレーターのスキームが示されています
図の 12.
顕著な層状形状を有する雲母を分離するには、スリット状のふるい面を作成するだけでは十分ではありません。なぜなら、雲母板がスリットを通過するには、雲母板がふるい面に対して垂直または斜めに配向されている必要があるからです。 この配向は、コーナー 1 から形成された屋根型スクリーン (図 2.5.2、a、b を参照) を使用して実現されます。この場合、ギャップを通過するマイカ プレート 2 の最大厚さ hmax は、隙間のサイズd c 垂直隔壁3を設置する場合、スクリーンスロットd cr を通過するマイカプレートの厚さが増加する。
したがって、ギャップを通過する雲母板の厚さ h は、コーナー 1 の棚の傾斜角 α または垂直隔壁 3 の高さによって決まります。 h = 直流sinα。
米。 2.5.2. 形式に従った濃縮のためのセパレーターのスキーム:
a - 屋根の形をしたスクリーン。 b - 垂直仕切りのある屋根型スクリーン。 c - 希薄化により平坦な粒子が保持されるドラムスクリーン。 g - 形状と風損を強化するための平面セパレーター。 d - 踏み台付きの棚セパレータ。 e - ベルト分離コンベヤー; g - 遠心分離機。」
α = 0 では、円形および長方形の粒子がふるいを通過します。 傾斜角αが増加すると、放出される粒子の厚さが増加し、npおよびα = 90°に達します。 h= d c 。
SM-13スクリーンは、面状の雲母(面原料)を得る主選鉱装置として、異形面を用いた形状別選鉱処理を行っています。 処理スキームは、埋蔵量、鉱石中の骨材の含有量、破片のサイズ(1; 0.6; 0.3 m)、結晶の面積、および採掘単位の生産性に依存します。 連殖の内容に応じて、鉱石は区別されます:最大5%-連晶が乏しく、5〜20%-平均、20%以上-連晶が豊富です。 上記の要因に応じて、単純な処理スキームと複雑な処理スキームが区別されます
形状による破砕と濃縮のための単純な技術スキームが、2 ~ 5 m 3 /h の処理量に使用されます。 生産性が高く、骨材中の鉱石が豊富であるため、形状による濃縮操作と外部特性による手動選別を使用して、原石炭を取得するための複雑なスキームが使用されます。 マイカの品質を維持するために、移動式マイカサンプリングユニット (SVU-1、SVU-2、US-1) を使用して処理されます。これにより、濃縮物の汚染が 6 ~ 20 未満の場合、最大 90% のマイカを抽出することが可能になります。 SVU-1、SVU-2 ユニットでは %、単純なスキームを使用して処理した場合は 20 ~ 70%。
分離される粒子の形状の違いから生じるいくつかの性質を利用する方法があります。 したがって、図では、 2.5.2、 Vドラムスクリーンは真空により平らな形状の粒子を保持し、そのシャフト3上にカップ状のふるい面2と円錐形のふるい面4が固定されている。 動力入力装置6と濃縮物出力装置7はドラムスクリーンの内側に取り付けられ、円錐形のスクリーン面4はシール8を備えたケーシング1によって覆われ、そのキャビティから空気がポンプで排出される。 ボウル型のふるい面からのふるい分けはトレイ 5 に集められます。
原料は供給シュート6を用いて椀状のふるい面2上に供給され、その上で細粒物質が篩下の生成物に分離され、丸くて平らな形状の粒子が単層で分布する。 スクリーンが回転すると、ボウル形部分 2 からの材料が円錐形部分 4 に入り、そこで丸い粒子がふるい上の製品に放出されます。 平らな形状の粒子は、円錐形のふるい面のかなりの部分を覆い、ケーシングの下から吸い込まれた空気の影響を受けて、ふるいの円錐面4に押し付けられる。 ドラム表面からの平板状粒子の分離は真空ゾーンの出口で行われ、雲母濃縮物は収集され、トレイによってドラムスクリーンから除去されます。
ドラムランブル粉砕された岩石から粒径 –300+0 mm の雲母を分離するのに使用でき、破砕後の丸い製品を再びスクリーンに供給して濃縮することができます。
平面セパレータ形状と風損を強化するために(図 2.5.2、d)、加速プラットフォーム 1、排出スロット、および反射突起が装備されています。 セパレータの特別な特徴は、ファン 6 が取り付けられているチャネル 5 の排出スロットに接続されている反射突起 3 の近くに穴の開いたプラットフォーム 2 が存在することです。プラットフォームの穴を通した空気の供給により、雲母が可能になります。粒子が反射突起に衝突し、アンローディング装置7を封止するためのスロット4からの空気取り入れにより、風損が増加した粒子、すなわち雲母がこのギャップに選択的に取り込まれることになる。 丸い粒子は突起 3 に衝突し、スロット 4 を通過してテール製品に入ります。
平らな粒子と丸い粒子の摩擦係数の違いとその風損は、 棚セパレータ(図 2.5.2、e)、粒径 5 mm 未満の雲母-花崗岩-石英混合物を濃縮することを目的としています。 それは、パラメータ(回転角度、長さ)を調整できる踏み台2で終わる傾斜棚1と、調整可能なゲートを備えた分離生成物の受け器とで構成されている。 マイカ受けはファンの吸込管に接続されています。 材料を分離機の棚 1 に供給するとき、ガーネットの回転とマイカの滑りの摩擦係数の大きな違いにより、踏み台 2 に近づく丸い粒子は平らなマイカ粒子よりも高い速度に達します。 踏み台 2 では、粒子速度が選択的に抑制され、ガーネット粒子とマイカ粒子の速度の差が大きくなります。 円形粒子と平板粒子の移動軌跡の違いや風損の違いにより、雲母粒子は雲母濃縮ホッパー内に偏向され、そこに堆積します。
棚分離装置の使用により、クレツキー鉱床の雲母含有頁岩から雲母濃縮物を得ることが可能になりました(図2.5.2e)。 マシンクラスを再加工する場合
1.35 + 0.7; -0.7 + 0.4; -0.4 + 0.25; -0.25+0.1 mm、雲母含有量 95 の濃縮物が得られました。 98.85; 96.5; 93.2%、回収率 8.2。 35.2; 19.3と24%。
の上 ベルトセパレーターコンベア(図 2.5.2、e を参照) 扁平な形状の粒子は、より平坦な軌道に沿って移動し、より長い距離を飛行します。 粒子の軌道は粒子の風損によっても決まります。 粒子の形状の違いにより、粒子の軌道が急激に変化(タンブリング)し、その結果、性能が低下することが観察されます。
で 遠心分離機(図 2.5.2、c を参照) 垂直軸に対する平らな粒子のねじれによる軌道の安定性を高めるための装置が提供されています。 分離器には、ディスク 1、速度 01 および 02 で回転するリング 2、および分離生成物のリング受け器が含まれています。 円盤とリングの回転方向は同じですが、リングの回転速度が速いため、平板粒子は円盤からリングに移動する際に垂直軸を中心にねじれて移動します。より安定したフラットな軌道に沿って。
これらには、手動による鉱石選別、放射選鉱、摩擦および形状選鉱、弾性選鉱、熱接着選鉱、および破砕中のピースのサイズの選択的変化に基づく選鉱が含まれます。
手選別(鉱石選別)は、鉱物の外観特性(色、輝き、形状)の違いを利用した選鉱方法です。 たとえば、マルタイト鉱石には、石灰岩の連続した包有物が含まれることがよくあります。 このような鉱石を粒径100mm以下まで粉砕することで、石灰石を容易に選別することができます。 鉱石の選別は材料サイズ 10 ~ 300 mm で、特別なプラットフォーム、固定および円形の可動テーブル、ベルトコンベアで行われます。 鉱石の選別に使用されるベルトコンベアは、18° 以下の角度で設置され、ベルト速度は 0.4 m/s 以下でなければなりません。 採掘エリアは十分に照明されている必要があります。 場合によっては、選別される鉱石の外観特性の違いを強調するように照明が選択されることがあります。 この方法は非常に高価であり、生産性も低くなります。 手動による鉱石選別は、高価な原材料(金、ダイヤモンドなど)の選鉱に使用されます。
特別な方法の中で最も広く普及しているのは、さまざまな種類の放射線を反射、放出、吸収する鉱物の能力の違いに基づく放射線濃縮です。
放射性濃縮は、非鉄金属鉱石(放射性、希少、重鉱など)、ダイヤモンド、蛍石鉱石の処理に使用されます。 放射濃縮のすべての方法の原理は同じです。宇宙を移動する鉱石は、放射線源からの何らかの種類の放射線の影響を受けます。 鉱物とこの放射線との相互作用から生じる信号が受信機によって捕捉されます。 情報は特別な装置の放射計に送信され、そこで処理されてコマンドがアクチュエータに送信され、アクチュエータがその情報を濃縮物収集または尾鉱収集のいずれかに送ります。 無関係な信号を遮断するために、回路にはフィルターが設置されています。 自動放射濃縮の場合、一次放射線源が必要ない(放射性鉱物自体が放射線を放出する)ため、スキームが大幅に簡素化されます。 最短のガンマ線から最長の電波まで、幅広い波長の放射線が一次放射線として使用されます。 波長に基づいて、放射分離器で使用される一次放射線の次のグループが区別されます。
鉱物と一次放射線との相互作用の性質に基づいて、次のグループが区別されます。 1) 二次放射線の励起 (発光、中性子など)。 2) 一次放射線の反射。 3)一次放射線の吸収(吸収)。
非放射性鉱石を放射濃縮する最も一般的な方法には、測光法と X 線ルミネッセンスがあります。
実装方法によれば、放射性濃縮は大部分の選別と放射性分離に分けられます。 最も安価で生産性の高い濃縮方法の 1 つである大部分の選別では、濃縮の対象となるのは個々の部品ではなく、ワゴン、ダンプ トラック、バケットなどです。 たとえば、自動放射分析法を使用した大部分の選別には、鉱石トラックの放射線の記録が含まれます。 放射線が一定の閾値を超えている場合(鉱石中に有用な放射性鉱物が多く含まれていることを意味します)、トロリーは工場で荷降ろされて濃縮され、放射線が閾値より低い場合(有用な成分が低い)、 、トロリーは直接ダンプに送られます。 この方法の欠点は、すべての鉱石に適用できるわけではないことです。 有用な(放射性)成分は、異なるトロリー間で不均一に分布している必要があります(含まれる量が少ないものもあれば、多く含まれるものもある)が、これは非常にまれに発生します。 放射分析による分離には、各鉱石の「観察」が含まれます。 この場合、非常に高度な技術指標が達成されますが、特に小さな粒子の場合、生産性が低くなります。
X 線発光法は、X 線放射の影響下での鉱物の発光 (コールド グロー) の強度の違いに基づいています。 発光プロセスは 3 つの段階で構成されます。励起放射線のエネルギーの吸収、励起エネルギーの体内への変換と伝達、鉱物の平衡状態への復帰による発光中心での光の放出です。 灰重石、蛍石、ダイヤモンドなど、多くの鉱物には発光する能力があります。ほとんどの鉱物の発光は、それらに含まれる活性剤不純物(発光原)の存在によるものです。
ダイヤモンド鉱石の濃縮には X 線発光法が主な方法です。 蛍石や灰重石鉱石の濃縮にも使用されます。 X 線発光分離器の一次放射線源は、さまざまな陽極 (タングステン、銅、銀、モリブデンなど) を備えた X 線管であり、これにより、特定の種類の原材料に最適な一次放射線を選択することができます。 セパレータでは、広い放射ビームを備えたチューブを使用することが好ましい。 さまざまな光電池や光電子増倍管が発光信号の受信機として機能し、光電池の種類は励起された発光の波長によって決まります。
ほとんどの放射分離器は同様の設計をしており、フィーダ、放射源 (自動放射分離器を除く)、記録装置、およびアクチュエータを備えています。 X 線発光分離器は、フィーダーの設計、材料供給モード、および部分の除去方法が異なります。 当社は、重力および浮選ダイヤモンド精鉱の仕上げやダイヤモンド鉱石の一次濃縮に広く使用されている LS シリーズ分離機 (図 2.23) を開発しました。 分離機には 2 つのフィーダーがあり、2 番目のフィーダーは最初のフィーダーよりも速く動作するため、分離機上の粒子は一列に引き込まれ、1 つずつ落下します。 粒子が発光できる場合(ダイヤモンド)、X 線放射の影響下で輝き始めます。 この輝きは光電子増倍管によって検出され、信号はアクチュエーター、たとえば空気圧バルブに送信され、空気流で粒子を吹き飛ばします。 海外製品の中でも注目すべきは、Hansons Sortex Limited (イギリス) が開発した XR シリーズのセパレーターです。
測光法は、光を反射、透過、または屈折させる鉱物の能力の違いに基づいています。 測光分離器の図を図 2.24 に示します。
摩擦と形状の強化。 傾斜面に沿った (特定の傾斜角での) 粒子の移動速度は、粒子自体の表面の状態、粒子の形状、湿度、密度、サイズ、粒子が移動する表面の特性、性質によって異なります。動き(回転または滑り)の変化、および分離が発生する環境。 傾斜面に沿った鉱物粒子の動きの観点から鉱物粒子を特徴付ける主なパラメータは摩擦係数であり、その値は主に鉱物粒子の形状によって決まります。 摩擦富化は、廃岩粒子と有用鉱物の摩擦係数の差が大きいほど有利となる。 粒子は、それ自体の重力 (傾斜面に沿って移動する場合 - 図 2.25)、遠心力 (回転ディスクの水平面に沿って移動する場合)、および重力、遠心力、摩擦の組み合わせの作用の影響下で移動します。力(スクリューセパレーター)。
これらの特性は、ダイヤモンド微粒子、アスベスト鉱石、雲母の濃縮、研磨材やその他の材料の分離に使用されます。
弾性による濃縮は、異なる弾性の鉱物粒子が装置の作業面から異なる方法で跳ね返り、異なる軌道に沿って移動するという事実に基づいています。 この方法は砂利の選別に広く使用されています。
熱接着選鉱法は、鉱石に光束を照射すると、濃い色の鉱物が明るい色の鉱物よりも加熱されるという事実に基づいています。 次に、表面が熱に敏感な材料(可塑化温度30〜50℃)で覆われたコンベアに乗ると、さらに加熱された濃い色の鉱物がこの表面に付着し、軽い鉱物は付着せず、その軌道に沿って移動します。 。 この方法は岩塩の濃縮に広く使用されています。
硬度による選鉱のプロセスは、鉱物原料を粉砕するときに、より柔らかい材料が破壊されるという事実にあります。 硬いものは大きな塊のまま残り、ふるいや分級機を使って小さな製品と大きな製品を分離します。 このプロセスは選択的粉砕と呼ばれます。 粉砕とふるい分けが 1 つの装置で組み合わされることがよくあります。 この方法は石炭の調製に広く使用されており、ドラムクラッシャーで実行されます。